Post written by Jesper of Shoegazing Blog
30 black oxfords, made by shoemakers from all over the world. Here’s a substantial review of all the competition shoes that entered the World Championships in Shoemaking. Info, comments, pictures of the shoes and in some cases also the manufacturing process.
Brace yourself, this is the largest post ever posted on this blog (and there’s been some really long ones, as many know), so large that it had to be divided into two posts, Wordpress couldn’t handle it otherwise. But hopefully one of the more interesting ones as well, for those who are into craftsmanship and the details of shoemaking.
Part of the London Super Trunk Show two weeks ago was the first World Championships in Shoemaking, organised by Shoegazing and The Shoe Snob. It was set-up in collaboration with online retailer Kirby Allison’s Hanger Project, book project Master Shoemakers, and private person Edmund Schenecker, who paid the substantial prize money of ?3,000 to winner, ?2,000 to second placed and ?1,000 to third placed. The top three shoes also will go on tour around the world now, to be showcased for as many shoe lovers as possible. The preliminary tour schedule is as follows:
w19-20 | May 7-20 | Leffot NY | New York, USA |
w22-23 | May 28-June 10 | Leffot Chicago | Chicago, USA |
w25-26 | June 18-July 1 | Kevin Seah | Singapore |
w28-29 | July 9-22 | Unipair | Seoul, South Korea |
w31-32 | July 30-Aug 12 | Medallion Shoes | Beijing, China |
w34-35 | Aug 20-Sept 2 | Prologue | Hong Kong |
w37-38 | Sept 10-23 | Skoaktiebolaget | Stockholm, Sweden |
w40-41 | October 1-14 | Isetan Men’s | Tokyo, Japan |
w43-44 | Oct 22-Nov 4 | Skomaker Dagestad | Oslo, Norway |
w46-47 | Nov 12-25 | Brogue Shoes | Geneva, Switzerland |

At the London Super Trunk Show all competition shoes were on display for the more than 800 people who visited the event during the day, and at the award ceremony in the evening top ten were presented. The shoes and the competition gained a lot of interest and admiration, and also afterwards the attention has been big. We are very happy that the shoemaking community also has accepted this competition, giving it and the contestants well-deserved recognition. It takes guts to send in a shoe for review and put your efforts on display like this. The day before the event the shoes were reviewed anonymously by the jury, which consisted of:
Jim McCormack, bespoke shoemaker
Nicholas Templeman, bespoke shoemaker
Keitaro Takano, bespoke shoemaker
Eric Devos, bespoke shoemaker
Patrick Verdillon, Director bespoke John Lobb Paris
Kirby Allison, founder of The Hanger Project
Gary Tok, author of Master Shoemakers
Jesper Ingevaldsson, Shoegazing
Justin FitzPatrick, The Shoe Snob

The criteria that were set out for the competition shoes were as follows:
Plain cap toe oxford model (at least three separate leather pieces, no wholecut with imitation stitches etc)
One left shoe, size UK8 (or corresponding size)
Black box calf upper
Single leather sole
Hand welted, handmade sole stitch
Black sole and heel edges, natural coloured bottom
No branding
Shoes were displayed without last or shoe tree for the jury (if shoe tree was provided these were only used when showcased during the event).
Competitors could enter both as a company or as a person. All persons that had been part in the making of the shoe should be stated, and which process(es) each person have made (we haven’t received full info on all competitors, but most).

The criteria that the jury reviewed, were the following:
Degree of difficulty (maximum 10 points)
Jury look at how complicated construction methods that have been used, how advanced they have been built both in large and in smaller details, etc.
Execution (maximum 10 points)
Jury look at how well the various parts of the shoe construction have been made, how neat and clean the work is, how well executed the level of finishing is, etc.
Design / Aesthetics (maximum 5 points)
Jury look at the overall aesthetics of the shoe, proportions, etc.
So, below first the full list of results, then a walkthrough of all competition shoes, from position 1 to 30 (1-10 in this post, 11-30 in another post). There’s more pictures and text on the top position shoes, but all have a brief summary and at least 5 pictures of the shoes in various angles. In some cases I’ve also included pictures of the making process. Click the pictures to see larger versions, to really get a look at some of the wonderful details that’s to be found.
Results (click on maker/brand to go directly to summary, go here for positions 11-30):
1. Patrick Frei Maßschuhe
2. Daniel Wegan
3. Philippe Atienza
4. Wataru Shimamoto
5. Fumiya Ando
6. Andreas Reijers
7. Kiyo
8. Christophe Algans
9. Christophe Corthay
10. Calzoleria Carlino
11. T.Shirakashi Bootmaker
12. Ruoda Zhao
13. Yuuki Homma
14. Antoine Besnard
15. Calzoleria Giacopelli
16. Elrod Shoes
17. Canale Bottier
18. Perticone
19. Stato Martinelli
20. Igor Suhenko
21. Valentin Frunză
22. Vass Shoes
23. euGO
24. Kenjiro Kawashima
25. Salon Lawart
26. Andrey Kaveshnikov
27. F&F Calzoleria Artigiana
28. BRR Shoemaker
29. Calzoleria Artigiana
30. Björn Fröding
Positions 11-30 can be found in this post.
.
1. Patrick Frei

The first World Champion in shoemaking is Patrick Frei from Germany. He has made the shoe entirely himself, spending 160 hours making it. The gorgeous shoe tree took another 40 hours, 20 from him and 20 by a professional violin maker who made the handle (note that the shoe tree was not part of the competition, only for the display). His shoe looks more like a museum piece than anything else. It’s a delicate take on the black plain cap toe oxford, even though the length corresponds to UK8, it’s very slim and neat, with a waist that is extremely narrow. It’s a shoe to look at, not to wear (similar to shoemaking contest back in the days, wearability is not necessary). The sole stitch is fine, 16 spi (stiches per inch), with a relatively rounded edge. Closing is well-made, though you can find some sections that aren’t perfect. The inside of the shoe is also thoroughly made, with fine details and complicated patterns.

The mentioned narrow waist is probably what attracts most attention when you first look at the shoe, and it is very nicely made, with super thin edges, clearly high-level of difficulty and good execution as well. However, three other parts was perhaps what impressed judges the most. First of all the heel, which is built of more than 20 extremely thin heel stacks, which also are nicely leveled. Extremely difficult to achieve this result, Patrick Frei used an old vintage sole leather which wasn’t the easiest to work with but which were excellent for the edge finishing and allowing a clean, neat heel to look at. Secondly, the nail pattern in the heel is very impressive, not only the amount of nails but also how straight he achieved the rows. Third is the toe tap, which is shaped by hand to a wingtip shape, perfectly trimmed together with the sole.

Patrick Frei’s shoe managed ot just take the number one position even though he received a 5% deduction of the total points, due to having the sole burned with a hot iron which made it more brown than he had planned (guidelines stated natural sole edge). It didn’t affect the possibility to see the sole work too much though (which was the purpose of asking for natural sole), hence only the 5% deduction, larger errors received a 10% deduction.

Patrick Frei is not a very well-known name in the shoemaking community, even though he has made shoes for 10 years time. He has an interesting background. He grew up in Freiburg in the very south west of Germany, close to the French border. When he was 18 years old, he quit school to travel to Spain and Morocco, where he started performing on the streets with juggling. After being back in Germany for a while to finish school he then headed to South America where he for several years worked as a juggling street artist, cycling from city to city, country to country. In Cochabamba, Bolivia I met an old craftsman who made these traditional, heavy but beautiful trunks and suitcases, where he gained an interest in leather craftsmanship, and also stayed for a while to learn some basics. He then went back to Germany, where his interest turned towards making shoes. He got a position as apprentice for a German master in 2005. He stayed there for 2,5 years, then started his own workshop.

Being young and self-confident, he thought he knew quite a lot about shoemaking. After seeing sample shoes made by Bavarian shoemaker Heribert Dirrigl, made to a superb standard which really blew his mind, he realised that he didn’t know much at all. He then spent several years gathering old shoe books, old shoes, visiting other well-renowned makers in Europe to continue to really learn. You can also see, not only in the World Champion shoe, but also his regular work, that he is very influenced by old vintage shoes. His workshop is located in the city of Blackforest in Freiburg, shared with leather crafstman Mathias Steinhauser. Patrick Frei’s regular bespoke shoes start at €5,000 (incl. VAT), including making of lasts, fitting shoes, three piece shoe trees. He does also offer what he calls Divine shoes, which are made more similar to the competition shoe (both art shoes, and shoes to be worn), where basically everything is possible to make and you pay per hour. Starting price here usually is around €13,000.
If you have the chance to visit any of the stores where Patrick Frei’s shoe, and the two runner ups, will be on display, do take the chance. It’s very inspiring looking at work at this level.
















We finish of this rather long section about the winning shoe with some pictures taken by Patrick Frei of the manufacturing process.
















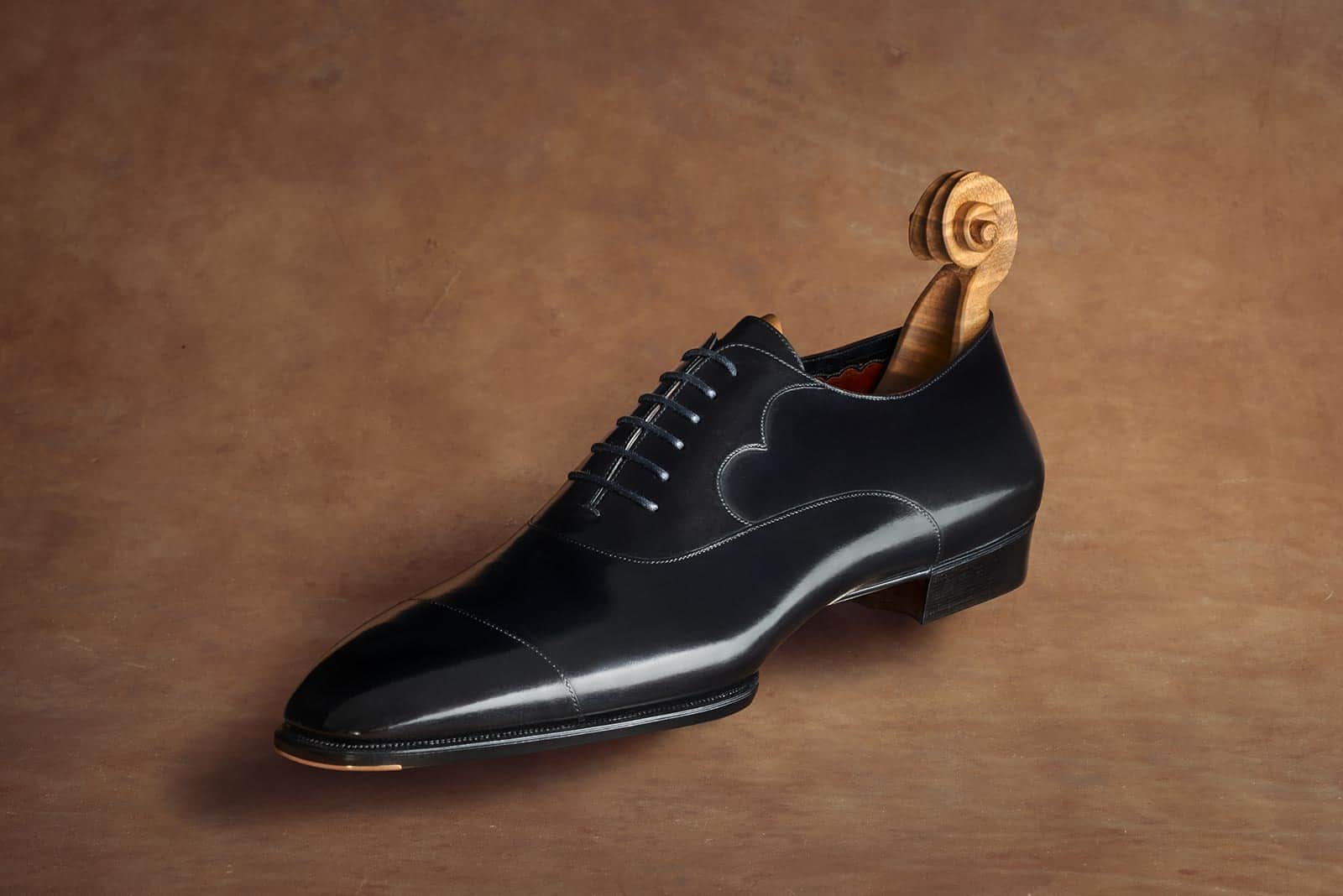
.
2. Daniel Wegan

Daniel Wegan, originally from Sweden, is head of the bespoke department at the famed British brand Gaziano & Girling. Daniel Wegan has made last and the making, while Kay Anderson, head closer of G&G, made the upper. This shoe really stands out with the high heel, inspired by shoes from the Victorian era, where also men’s shoes were high heeled like this. Though maybe not to everyone’s taste aesthetically, no one can deny the superb craftsmanship and high level shoemaking that has gone into this shoe. The total points for execution were on par with Patrick Frei’s shoe, though the latter received higher points on aesthetics and especially difficulty, That said, Daniel Wegan’s shoe surely has some complicated parts as well, not least with the sole stitch of an impressive 21 spi (stitches per inch). It’s actually so perfectly, made with a thin thread and neat fudging, that some people who saw the shoe at the super trunk thought it was imitation welt (only decorated welt, no stitches).

In general this shoe is made with a refined finesse, it looks so natural, so made with ease. That type of shoe that can really take a close examination. From the perfectly leveled heel stacks to the excellent closing of the upper made by Kay Anderson. Waist is also more narrow than usual, with the blind welted edge very nicely executed. The making is, apart from the sole stitch, more of a very well-made bespoke pair for customers, than the artistic approach made by Patrick Frei or some of the French guys.

For those who don’t know about Daniel Wegan, he is one of the wonderchilds of the bespoke shoe world. He wanted to learn how to make shoes, so he moved to England eight years ago and went knocking on the doors of the shoemaking firms in London and Northampton to find a job. Gaziano & Girling let him in, where he swapped the floors and helped out in the factory, in exchange of time to follow the making in the bespoke department. He started trying things out, and after a while was allowed to do some repairs on their bespoke shoes. Evenings, nights and weekends he spent making shoes in his apartment. He soon worked full time in the bespoke department, learned lastmaking, and has now since several year’s been the manager of the department. He is employed as Head of the bespoke department and lastmaker, this is his dayjob, then still in the evenings and weekends he works as freelancer for G&G and do bottom making in the “small factory”, his apartment (where three out of four rooms, plus kitchen, are workshop areas). Learn more about Daniel and Gaziano & Girling bespoke in the article series following a bespoke order from start to finish, found under the headline Bespoke on this page.












Also here we have a few pictures of the manufacturing process.






.
3. Philippe Atienza

Philippe Atienza started his own brand only a couple of year’s ago, but he has been working in the French bespoke shoe industry for several decades. He has made all parts of the shoe. With his shoe he combines a classic French last shape and making, with a slightly special pattern of the quarters which makes it easily recognisable. It’s not as elegant, neat and delicate (which doesn’t have to be purely positive) as the two previous shoes, but they are very solidly built.

The sole stitching is at 12 spi (stitches per inch), with a very distinct fudging (when a fudge wheel is used to place and press the stitches, which creates the decorative pattern on top of the welt) and slightly wider edge which really draws your eyes to this well-made part of the shoe. This together with the relatively solid heel contrasts beautifully against the the close-cut edges at the waist area. The sole and waist may look a bit plain at first, but it’s also what makes it good, it’s nothing more than a very well-executed shoe bottom.

Philippe Atienza is really a grand old man within bespoke shoemaking. Already back in 1978, when he was 16 year’s old, he began the French craftsmanships education programme Les Compagnons du Devoir, where he apprenticed with various shoemakers during several years. At the age of 20, he took part in building up a a workshop for orthopedic shoes outside Paris where he worked for some time. He then did a session at a shoemaker in Marseille and one in Strasbourg, before returning to Paris and starting a long employment for John Lobb Paris. During his years there he worked both with bottom making, closing and were workshop manager. In 2006 he left Lobb to take on the position as Managing Director of the bespoke firm Massaro (owned by Chanel), who makes both men and women’s shoes. Then two years ago he started his own brand, Philippe Atienza Bottier, having a workshop in central Paris. A report about Philippe Atienza will be published here on Shoegazing later this year.











.
4. Wataru Shimamoto

Wataru Shimamoto is, as the name might hint, from Japan. He has been learning shoemaking in Italy, and is since many years been based in Florence, where he works as a bottom maker for Hidetaka Fukaya’s brand Il Micio. Since the shoe made isn’t a classic plain cap toe oxford model, but a plain cap toe oxford balmoral, the shoe has received a 10% deduction of the total points. Even so, Wataru Shimamoto managed to end up in fourth place. Cause the shoe is really superb, made on perhaps the sleekest and sharpest lasts of all competition shoes. The last shape clearly reminds a lot about Il Micio’s lasts.

The degree of difficulty is good, though not the highest in the contest. However, the execution of the making is excellent. Flawless sole stitching and welt treatment, perfectly shaped blind welted waist edges, gorgeous transition between heel and upper. There’s some areas where it’s not as perfect, closing is made with tight stitching but has some places where it’s a little bit off, and some heel stacks are slightly wavy. All in all though, still a pleasure to watch this shoe.






.
5. Fumiya Ando

Japanese Fumiya Ando has only made shoes for three years, making him a “beginner” compared to most of the other highest placed shoemakers. He has made the whole shoe himself. It’s a very well-balanced shoe, slightly bulbous yet elegant and smooth on the eye. Degree of difficulty was rated slightly higher than execution, and it received good points overall on design. It has the blind-welted bevelled waist, very close-cut heel, good sole stitching, and so on. However, you can find things like a small glitch between two of the heel stacks, not perfectly trimmed upper edge of the heel, slightly wavy welt upper.

Fumiya Ando studied art in Tokyo after he had finished high school and made some work as a contemporary artist. He had a big shoe interest, and then went over to learn shoemaking at one of Tokyo’s shoemaking schools. He is now in the process of setting up his own brand. With the kind of work that his competition shoe is already, he is surely a name to keep an eye on.






Here are a few black and white photos of the manufacturing process.




.
6. Andreas Reijers

The Swede Andreas Reijers is also relatively new in this business, starting making shoes a bit over three years ago, and has up until recently worked for Gaziano & Girling. He has made the last and bottom making, while Northampton based closer Selahattin Cebeci made the upper. This is another one of these very well constructed, elegant classic models. The making is splendid, closing of the upper has some flaws though, some execution points were lost here.
Several things are really exemplary on the shoe, like how well he has made the heel stand out as a separate part, with a distinct notch towards the waist and slightly elevated top. The proper fiddle back waist is narrow and beautiful, and though sole stitching not is the tightest of the bunch, its nicely marked with clean work with the fudge wheel.

Andreas Reijers grew up in Sweden, but moved to Norway in the early twenties, where he worked as a chef. He saw films of shoemaking on YouTube, which amazed him, and went try his luck at a school for cobblers in Norway. Repairs was not for him though, he wanted to make shoes. So he moved to Northampton in England, started working in the Crockett & Jones factory during daytime and learning bespoke shoemaking from his friend Daniel Wegan in nights and weekends. About 1,5 years ago he got a full time job with Gaziano & Girling and worked as a maker for them. Recently he moved back to Norway though, but plan is to continue making shoes from there, which we really hope he does. Such talent should not go to waist.







And also here some pictures of the making process.







.
7. Kiyo

Kiyo, or Kiyo Uda as is his full name, is a bespoke shoemaker based in Tokyo. He has made it all by himself, even the accompanied shoe tree (not part of the contest). The shoe has a slightly special look, a sort of mix between elegant and more bulbous shapes. The balance with the low placed waist and slightly higher toe spring is perhaps not to everyones liking. It’s well made, no special things, but done as it should be. Apart from the inside of the shoe, should be mentioned, which did affect the points given a bit (it was stated that the shoes should be reviewed without lasts or shoe trees, which means that we of course also looked at the inside of the shoe).

Kiyo is 33 years old and started a shoemaking school in Tokyo about nine years ago. After two years there, he moved to Europe and England, where he worked as a bottom maker for George Cleverley. He has now moved back to Tokyo, where he makes shoes under his own name and also work as a freelance maker for other Japanese bespoke shoe brands. He is one of many relatively unknown highly skilled Japanese bespoke shoemakers.






Making pictures taken by Kiyo in his Tokyo workshop.



.
8. Christophe Algans

Frenchman Christophe Algans has really made an artistic and experimental take on the plain cap toe oxford, balancing on what can be allowed, but do follow the guidelines. He has worked with bespoke shoes for more than 25 years, most of them at Corthay in Paris alongside Christophe Corthay (which will be very evident when you see the next shoe below made by the latter).

The playfulness developing this shoe is inspiring, and you can look a long time on all the details. The sharp 90? sole edge at the toe, the completely assymetric pattern, the silver laces matching the lining leather, the sketch of a woman on the waist, and of course the horse shoe heel shape. For sure not a shoe for everyones taste, but you can’t deny its creativity. A lot of difficult parts on the shoe, not always made to perfection perhaps, the finish on things are a little bit rough.






.
9. Christophe Corthay

Christophe Corthay, France, (who have made the entire shoe himself) is one of the most famous names of the contest. Having worked alongside his brother Pierre with Maison Corthay for several years, he left to continue on his own a few years ago. He has been working on the project Tranchet Vif, of which we can see a lot of similarities to the competition shoe, which is sent in under his own name. A real rock’n’roll shoe, with several really complicated processes. For example, at a first glance on the shoe, the sole edge may look really wide and stitching sloppy. When you look closer, you realise that the sole stitching is actually braided in a very impressive way.

Similar to Patrick Frei, he got a 5% deduction of the total points for not making the sole fully natural coloured. That said, it’s quite an awesome bottom, with a whale painting, an insert with different leather material in the waist, and also here a horse shoe heel. He has used peaks as a design element throughout the shoe, and worked some with asymmetry especially at the lacing area. It’s not the most clean making, although still on a good level. The leather may look a bit bad, it’s only due to cracked layers of polish, the shoe had a high shine all over and when we struggled a bit to remove the shoe tree for the jury review the polish cracked. This has not been something that inflicted with the judging.







.
10. Calzoleria Carlino

Riccardo Carlino is a young Italian shoemaker, only 24 year’s old, behind the brand Calzoleria Carlino based in Modena. He received a 10% deduction on the total points for the black waist and heel bottom, which was against the guidelines. The making of the shoe is really top notch, not that Italian in style, more of a classic British bespoke shoe. The waist is pulled in far on both sides of the shoe, slim with a pronounced fiddle back. It has created some heavy awl marks when working on the sole stitch, could have been avoided by going in with the awl from the bottom instead, which would have created a cleaner looking waist here.

Sole stitching, welt finishing and heel building is all neat and clean. In terms of design it’s as mentioned very classic, but has some nice small details like the nail pattern on the heel and the stitching along the facing which curves in lovely along the opening.




